Concrete plywood is an essential component in many construction projects, providing a strong and durable material for various applications. When it comes to choosing the right concrete plywood for your project, there are several factors to consider. Understanding the basics of concrete plywood, the different types available, and proper installation techniques can help you make an informed decision. Additionally, regular maintenance and care are crucial for ensuring the longevity and performance of your concrete plywood.
Understanding the Basics of Concrete Plywood
Concrete plywood, also known as formwork plywood or forming plywood, is a specialized type of plywood designed for use in concrete formwork systems. It is used to create temporary molds or forms that hold wet concrete until it hardens and gains sufficient strength. These forms provide support and structure, allowing the concrete to take the desired shape.
Concrete plywood is an essential component in the construction industry, particularly in projects that involve intricate designs or custom shapes. Its versatility and durability make it a preferred choice for contractors and builders looking to achieve precise and high-quality concrete finishes.
What is Concrete Plywood?
Concrete plywood is made by bonding multiple layers of wood veneers with water-resistant adhesive. The outer layers are typically treated with a special overlay material that enhances the durability and smoothness of the plywood surface. This overlay also improves the release properties, making it easier to remove the plywood from the hardened concrete.
Furthermore, the use of high-quality concrete plywood ensures that the concrete surface remains free from blemishes and imperfections, resulting in a flawless end product. Its ability to withstand the pressure exerted by wet concrete and the curing process makes it a reliable choice for construction projects of all sizes.
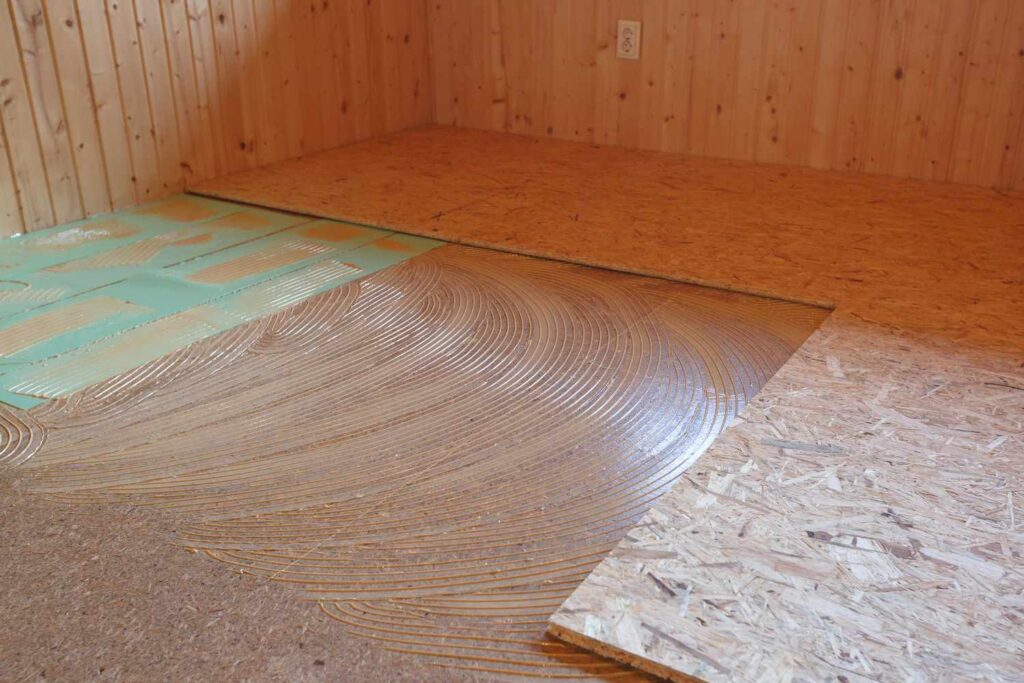
Importance of Concrete Plywood in Construction
Concrete plywood plays a crucial role in construction projects, especially for structures that require custom shapes or intricate designs. It provides the necessary support and stability during the concrete pouring and curing process. Additionally, concrete plywood helps achieve a smooth and uniform finish, improving the overall aesthetics of the project.
Moreover, the precise engineering and manufacturing processes involved in creating concrete plywood ensure consistent quality and performance. This reliability is paramount in construction, where any compromise in materials can lead to costly delays and structural issues. By investing in high-grade concrete plywood, builders and contractors can ensure the success and longevity of their projects.
Factors to Consider When Choosing Concrete Plywood
Choosing the right concrete plywood involves evaluating various factors to ensure optimal performance and longevity. Here are some key considerations:
Read more: Concrete Form Plywood Key Features and Benefits
Durability and Strength
Concrete plywood should have excellent durability and strength to withstand the pressure from the wet concrete. Look for plywood that has undergone proper treatment and has high structural integrity. A higher grade plywood, such as B-B or B-C, is recommended for enhanced durability and longevity.
Additionally, consider the type of wood used in the plywood. Hardwood plywood, such as birch or oak, is known for its strength and durability, making it a popular choice for concrete formwork. Softwood plywood, like pine, is more budget-friendly but may not offer the same level of durability.
Resistance to Moisture and Decay
Since concrete contains water, plywood in contact with wet concrete needs to have good moisture resistance. Moisture-resistant overlays, such as Medium-Density Overlay (MDO) or High-Density Overlay (HDO), provide added protection against water damage and decay. These overlays also help improve the smoothness of the concrete surface.
Furthermore, consider the environmental conditions the concrete plywood will be exposed to. If your project is in a high-humidity area or will be subjected to frequent wetting, opting for a phenolic surface film on the plywood can provide superior protection against moisture and prolong the lifespan of the formwork. Read more about lifespan on https://opentext.wsu.edu/psych105nusbaum/chapter/what-is-lifespan-development/
Size and Thickness
The size and thickness of the concrete plywood also play a crucial role in determining its suitability for your project. Consider the dimensions of the forms and ensure that the plywood panels are large enough to accommodate them. Thicker plywood panels offer better stability and can handle heavier loads during the concrete pouring process.
Moreover, thicker plywood can help prevent deflection or bending during the concrete placement, ensuring a smooth and even surface finish. It is essential to balance the thickness of the plywood with the spacing of the formwork supports to prevent any flexing that could affect the quality of the concrete structure.
Different Types of Concrete Plywood
There are several types of concrete plywood available in the market, each with its unique characteristics and applications. Here are some common types:
Medium-Density Overlay (MDO) Plywood
MDO plywood has a high-quality resin-impregnated overlay that provides excellent durability and moisture resistance. It is commonly used for concrete formwork where multiple reuses are expected. MDO plywood also offers good dimensional stability and a smooth surface finish.
One of the key advantages of MDO plywood is its ability to maintain its shape and strength even under heavy concrete pouring pressures. This makes it a popular choice for contractors working on projects that require precision and reliability. Additionally, the smooth surface of MDO plywood allows for easy release of the concrete after curing, reducing the need for additional finishing work.
High-Density Overlay (HDO) Plywood
HDO plywood is known for its superior surface performance and resistance to moisture and abrasion. It is ideal for projects that require a high-quality finish and high-reuse applications. HDO plywood is suitable for use in demanding construction projects like bridges, buildings, and tunnels.
Due to its exceptional durability, HDO plywood is often chosen for projects in harsh environmental conditions where regular plywood might not withstand the elements. The high-density overlay on HDO plywood provides a protective barrier against water, chemicals, and other potential sources of damage, ensuring the longevity of the formwork and the quality of the concrete surface.
Structural 1 Plywood
Structural 1 plywood is a specialized type designed for applications that require higher strength and stiffness. It is commonly used in heavy construction projects where the plywood forms need to withstand heavy loads and pressures. Structural 1 plywood can be reused multiple times and provides excellent structural stability.
Engineered to meet stringent performance standards, Structural 1 plywood is favored for its ability to support heavy concrete loads without bending or warping. Its reliable strength makes it a go-to choice for large-scale construction projects such as industrial facilities, parking structures, and high-rise buildings. The consistent quality of Structural 1 plywood ensures that the concrete forms maintain their integrity throughout the pouring and curing process, resulting in structurally sound and visually appealing finished structures.
Proper Installation of Concrete Plywood
To ensure the successful installation of concrete plywood, proper techniques should be followed. Here are some essential installation steps:
Preparing the Surface
Before installing the concrete plywood, make sure the surface is clean, level, and free from debris. Smooth any rough edges or imperfections that could affect the quality of the concrete finish. Proper surface preparation is crucial for achieving a seamless and uniform concrete surface.
Additionally, it is recommended to apply a bonding agent or primer to the surface before placing the concrete plywood. This will enhance the adhesion between the plywood and the concrete, resulting in a stronger bond and improved overall performance.
Installation Techniques
Start by securing the concrete plywood panels securely to the supporting structure. Use appropriate fasteners, such as nails or screws, to ensure stability. Pay special attention to the joints between the panels, ensuring a tight and flush fit. Properly aligned and well-connected plywood panels are essential for maintaining the integrity of the concrete formwork.
Moreover, consider adding additional support, such as bracing or shoring, especially for vertical installations or large surface areas. This extra reinforcement will help prevent any sagging or shifting of the plywood during the concrete pouring and curing process, ensuring a smooth and even concrete surface. To learn more about bracing click here.
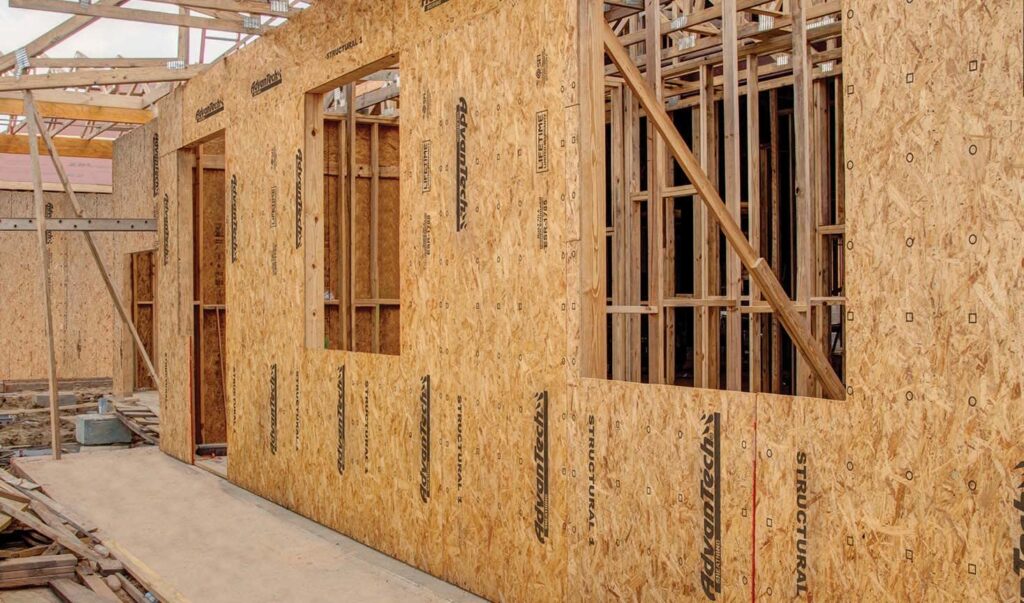
Maintenance and Care for Concrete Plywood
Maintaining and caring for your concrete plywood is essential for extending its lifespan and ensuring optimal performance. Here are some maintenance tips:
Regular Inspection
Periodically inspect your concrete plywood for any signs of damage, such as cracks, warping, or delamination. Address any issues promptly to prevent further deterioration. Regular inspections help identify potential problems and allow for timely repairs or replacements.
Cleaning and Repair
After each use, clean the concrete plywood carefully to remove any residual concrete or debris. Use mild detergents and avoid harsh chemicals that could damage the plywood surface. If any damage occurs, repair it promptly to maintain the strength and integrity of the plywood.
Choosing the right concrete plywood is vital for the success of your construction projects. Consider factors such as durability, moisture resistance, size, and type when making your selection. Follow proper installation techniques and ensure regular maintenance and care. By doing so, you can ensure a strong and reliable foundation for your concrete structures, achieving the desired results for years to come.
Additionally, it is important to note that concrete plywood is a versatile material that offers various benefits. It provides a smooth and stable surface for concrete pouring, ensuring a level and consistent finish. The plywood’s strength and durability make it suitable for both residential and commercial construction projects, offering long-lasting performance and reliability.
Furthermore, proper storage of concrete plywood is crucial to prevent damage and prolong its lifespan. Store the plywood in a dry and well-ventilated area to avoid moisture absorption, which can lead to warping or delamination. Stacking the plywood properly and using supports to distribute weight evenly can prevent bending or deformation, preserving its structural integrity.